TRC for self-sufficient living
Table of contents
Project data
Titel | Title Wachstumkern Autartec – Verbundprojekt 1: Funktionsintegrierte Bauelemente aus Textilbeton, TP 1.6: Experimentelle Untersuchungen zur Prüfung und Entwicklung von Materialien im Bereich des Textilbetons sowie funktionsspezifische Bauteilprüfungen an Textilbetonelementen | „Wachstumkern Autartec“ – Joint research project 1: Functional integrated construction units made of textile reinforced concrete, TP 1.6: Experimental investigations for the development and testing process of textile reinforced concrete materials and component testing for textile reinforced concrete construction units Förderer | Funding Bundesministerium für Bildung und Forschung (BMBF) / Wachstumskern autartec® Zeitraum | Period 09.2014 – 08.2018 Leiter | Project manager Prof. Dr.-Ing. Dr.-Ing. E.h. Manfred Curbach Bearbeiter | Contributor Dipl.-Ing. Egbert Müller Projektpartner | Project partners AIB GmbH, Bautzen | bendl HTS, Sebnitz | BWB, Sebnitz | DZT, Dresden | Rupp Betonerzeugnisse, Neustadt an der Orla |
Report in the annual report 2018
AUTARTEC® – CONSTRUCTION PHASE STARTED
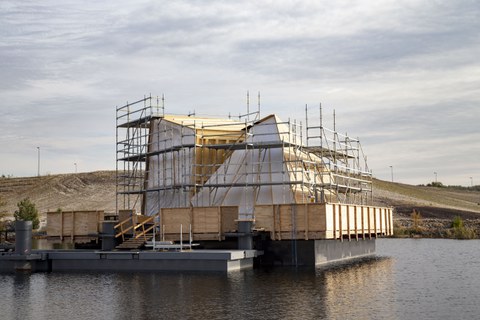
Außenansicht des autartec®-Hauses
From 2014 to 2017 every technology module of the autartec® house was designed, tested and finally manufactured. This year the construction phase of the autartec® house has begun on lake Bergheider in Brandenburg. Building the pontoon of the swimming house has been the first step, afterwards a bridge was build which connects the house and the mainland. Next, a frame construction made of wood was built on top of the pontoon. At first, a steel frame was planned, but due to the additional amount of dead load the planners in charge chose wood.
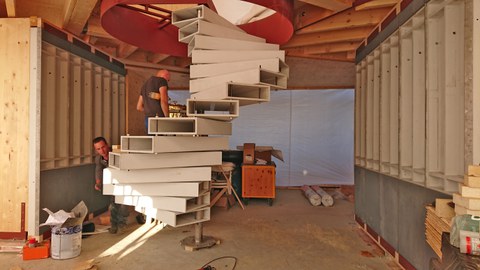
Wand- und Treppenelemente aus Carbonbeton
By building the framework a very important milestone was reached. The roofing ceremony was celebrated with the participation of all project members. This day of pleasure and relaxation refilled the energy reserves and raised the motivation to proceed the work. First, bendl HTS constructed the carbon reinforced concrete wall elements. To prevent the wall elements from turning over they were connected by a guide rail. From a static point of view, the wall elements have no task, however, laboratory experiments showed that they are able to bear capacities up to the weight of an ICE railway carriage. Later in the construction phase technology modules and doors will be installed in the wall elements. Therefore each damaged technology module can be repaired or replaced easily without removing the whole wall element.
Compared to the wall elements the filigree stairs have to transfer the bearing loads to the foundation. The steps were lifted to the second level by a crane and threaded carefully on a steel spindle. To receive a better load transfer and to fix their positions and prevent displacement the steps were linked to each other. The steel spindle will be connected with both the ceiling construction in the second floor and of course the base plate to obtain better stiffness and stability. Finally, a handrail will be installed to complete the stair system and release it for use.
Report in the year book 2017
AUTARTEC® – LET’S GO SWIMMING
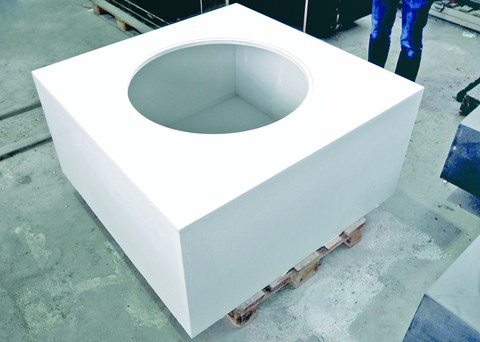
Prototype of a carbon reinforced concrete pontoon
Three years of research and development have gone by, and it’s time to start building the autartec® house demonstrator. Every single technology module is developed and optimized and will be ready to be installed in 2018. Within the frame of the common research project 1, a small-scaled pontoon was designed and produced. Its suitability was checked based on the knowledge gained during the development of the wall and stair elements. This first step is meant to show the feasibility of a carbon reinforced concrete pontoon, which could be implemented in the future as a variation of the system, yet the autartec® house will be still built of pontoons made of steel.
The wall and stair elements were designed using a “slab with web stiffeners” construction concept. Good results were reached, e.g., for the load bearing behaviour, and therefore this construction concept was applied to build the pontoon. Besides the load bearing resistance of the pontoon, the floating stability is really important and has to be considered during the design. To guarantee the floating stability, the centre of gravity of the pontoon should primarily be beneath the surface of the water. The small scaled pontoon is designed to carry a technology module with a weight of 300 kg. The cross section of the bottom slab has a square shape, with a side length of 1.25 m, the depth is 0.625 m, and the thickness is only 2.5 cm. Therefore, the centre of gravity of the pontoon is located at about half of its depth due to geometrical symmetry. Without the weight of the technology module, the pontoon immerses only 20 cm. Taking into account the weight of the technology module, the pontoon dives 40 cm into the water, and the centre of gravity of the pontoon is below the water’s surface.
Due to the technology available to produce this first small pontoon, the stiffener webs were not included. Also, the pontoon was produced without any construction joints. To produce a pontoon without any joints, a special formwork, made of wood, was necessary. This formwork was removed very soon to prevent damage due to the concrete’s shrinkage. The results of the first test pontoon were very satisfactory, as it can be seen in the pictures. The floating stability was tested at the laboratory of Prof. Stopp at BTU Cottbus-Senftenberg, and we would like to take this opportunity to express our gratitude to all of them.
Report in the year book 2016
Autartec® thinking for the future
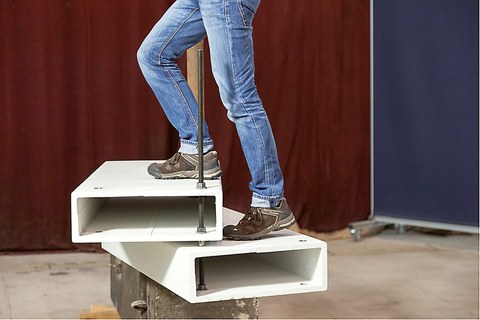
Prototype of the steps made of carbon reinforced concrete
After developing the basic design of the autartec® house during the first year, the autartec® design was optimized in a series of iterations during the second year. A considerable progress in planning was made, and many of details were conceived and presented, including changes proposed by all involved partners. Numerous discussions relating to such optimizations were necessary to reach a milestone in building a concept for future autarkic houses, which will be placed in open waters or seascapes.
First, along with the industrial partner AIB Bautzen, we designed a wall element. In 2015, the first elements were constructed with a carbon reinforcement based on a styrene-budatiene rubber coating. For a more efficient manufacturing process, the new carbon reinforcement is based on an epoxy resin coating. An advantage of the carbon reinforcement with the new coating is the possibility of prefabrication of special reinforcing elements such as corner reinforcements. Both types of wall elements were tested successfully in lab tests, regardless of the coating system used.
In 2016, the second year of the project, our main task was to construct an entirely new staircase system. Not only did the static conditions have to be met, but space to install technology modules were considered in the design as well. Accounting for all these facts, we believe that a cellular concrete box is the right cross section for this type of stair element. The bearing of the stairs is fixed to a steel spindle on one side, and it is connected with the handrail and to the steps above and beneath it on the other side. A spacer is placed between the stair elements. Due to the lack of a general standard, lab test were made. Our goal was to apply a load of 2 kN one million times. The static system in the lab tests was a cantilever, which is worse than the static system in practical application. The load was applied at the location with the largest lever arm, and not along the walking line. The tests of stair and of wall elements were a success.
In the last quarter of 2016, all documents were submitted to the inspecting structural engineer. After the structural analysis checks were completed, the construction approval to start building the autartec® house was granted. At this point, the house will be built at the Bergheider See in Germany in the late summer of 2017.
Report in the year book 2015
autartec – the building design is done
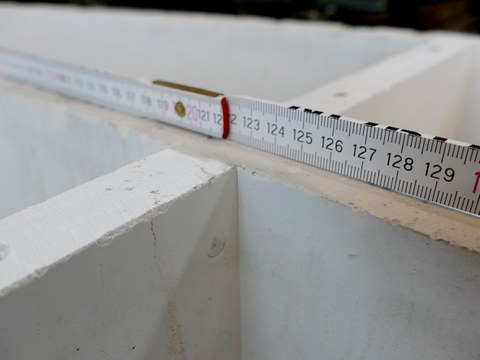
Detail of the TRC wall element
A huge milestone of tomorrow’s buildings is the autarkic efficiency. The research project `autartec` will make an essential contribution to achieve this goal. One third of the project has been completed, as scheduled, in a timely manner, and we can proudly present the final building design. To ensure a highly effective degree of self-sufficiency, both the photovoltaic system and the solar thermal system are optimized for the winter months. During the summer time, the cooling system works with an economical evaporating unit, which can be activated according to one’s requirement.
To guarantee the basic supply of electricity, thermal energy, and potable water, many technology modules, comprised of control systems and equipment, are necessary, needing a big amount of storage space. One goal of the research project is to place most of the required modules in the structural elements of the building. In addition, every structural element shall be accessible and opened for maintenance or replacement of the components.
One of such structural elements is a wall element. Basically, this wall element is a ribbed construction with additional cross webs to increase the stiffness of the cross section, and a removable façade, when required. The manufacturing process will focus on producing precast elements for this purpose. Besides having no construction joints, another advantage of the precast approach is the smooth surface of the wall element. On the basis of a smart element design, the textile reinforcement consists of many reinforcement cages. To handle the installation and an accurate placement of the reinforcement, the reinforcement cages are modified with an epoxy resin. In this manner, the geometrical stability of the reinforcement is ensured. Now, with the help of spacers, the reinforcement cages can be installed in the framework easily.
After the completing the manufacturing process of the wall elements, studies of the thermal and sound behaviour were carried out. The isolation of the wall elements to the floor construction and to each other is being taken into consideration at the present time. In addition, the load-bearing capacity was determined at the Otto-Mohr-Laboratorium. Control systems and equipment installed within the walls require tight temperature control at the wall voids used as storage. Our next task is to develop and study a modular staircase system.
Report in the year book 2014
Autartec – Living on the water
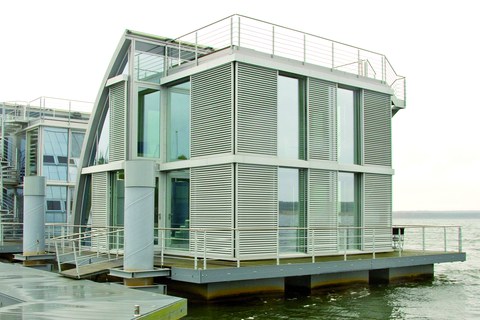
Already existing floating homes in steel composite construction on the future site
The next generations of civil engineers have to consider energy efficiency in both areas: structural design and living conditions. To meet these requirements, a solid research is necessary. Today’s buildings can be roughly divided into three groups: traditional, semi-autarkic and self-sufficient constructions. A self-sufficient building needs a lot of room for utilities, and, as result of this, the living space is reduced. This scenario needs to be changed.
One big step towards a self-sufficient construction was reached by the ground-breaking research on textile reinforced concrete (TRC). With this new composite material, it’s possible to generate thin and filigree structural elements. A feasible use of such elements could be a double U-channel. This type of TRC-element provides cavities which can be used to place and store all the technology media required for a self-sufficient construction.
In a self-sufficient construction, the replacement of each individual element has to be guaranteed. Furthermore, the cost and lifetime of several components need to be taken into consideration. Therefore, the TRC-elements have to be efficiently designed and arranged. All of these facts are important to bear in mind during the planning phase of such a kind of construction. Additionally, with regard to comfortable living conditions, all the conventional requirements, e. g. of thermal insulation, sound insulation and air tightness, must be met. To reach this goal, project partners from several disciplines work together. We can hardly wait for the first results from each member involved in this cooperative effort. After three years, the developed components for a self-sufficient construction will be installed in a model house, to be located in the Lausitzer Seenlandschaft. Furthermore, this structure will be used to monitor the long-term behavior of the installed components. The public will get the opportunity to take a look into this showcase construction.