Promotionsprojekt 11: Methodische Entwicklung aktiver Multi-Matrix-Verbund-(MMV-)Komponenten
Inhaltsverzeichnis
Motivation
Zur Erzeugung von 3D-Verformungen, die durch eine elastische Verformung ihrer Glieder einem definierten Weg folgen und/oder Kraft übertragen, sind so genannte bahnerzeugende nachgiebige Mechanismen im Forschungsbereich dieses PP. Die vielfältigen Anwendungsmöglichkeiten derartiger Compliant Mechanismen erfordern die Entwicklung einer systematischen Methode für den Entwurf und die Herstellung solcher Strukturen.
Stand der Forschung und eigene Vorarbeiten
Die in der 1. Kohorte erarbeiteten Auslegungs- und Syntheseverfahren für Komplanar-Wirkende-(KW-) Compliantstrukturen mit werkstofflich integrierten Antriebselementen sind auf sog. Nicht-Komplanar-Wirkende-(NKW-)Mechanismen zu erweitern. Hierbei werden gezielt werkstoff- und strukturbasierte Anisotropieeffekte ausgenutzt, die eine Kopplung innerhalb des Verzerrungstensors bewirken. So lassen sich räumliche Bewegen aus ebenen Anregungen ableiten. Die – bereits im Rahmen des SFB 639 – vorbereiteten Ansätze für textilverstärkte Strukturen [1] sind hierfür zunächst zu verallgemeinern und auf generische Führungsmechanismen mittels anwendungsgerechter Auslegungswerkzeuge anzupassen. Die Erstellung eines Berechnungstools zur Erzeugung solcher Strukturen ist durch den Einsatz von genetischen Algorithmen möglich. Die wenigen in der Literatur verfügbaren wissenschaftlichen Arbeiten [2, 3] zu diesem Thema berücksichtigen jedoch keine direkt in die Struktur integrierten Aktoren. In diesem Bereich besteht somit ein großer Forschungsbedarf.
Wissenschaftliche Fragestellung und Projektziele
In der 2. Kohorte soll das entwickelte integrale Konstruktions-Berechnungsmodell auf dreidimensionale Verformungen erweitert werden. Dafür ist zunächst die grundlegende Strukturanalyse auf die Mikroebene auszudehnen, da nur so eine gezielte lokale Werkstoffadaption während der iterativen Konstruktionsphase möglich wird. Um den gesamten iterativen Konstruktions- und Herstellungsprozess vollständig zu automatisieren, sind angepasste Schnittstellen zwischen der Berechnungsumgebung und der CAM-Software zu entwickeln. Die Validierung der Ergebnisse beider Pfade (3D-Mechanismen + 2,5D-Mechanismen) ist durch die Herstellung eines Multi-Material-Mechanismus mit integrierten textilbasierten Aktoren und Sensoren durchzuführen. Hier hat sich die additive Fertigung, als effiziente Methode zur Herstellung der Demonstratoren bewiesen.
Literatur
[1] | KOCH, I.; ZSCHEYGE, M.; GOTTWALD, R.; LANGE, M.; ZICHNER, M.; BÖHM, R.; GRÜBER, B.; LEPPER, M.; MODLER, N.; GUDE, M.: Textile-Reinforced Thermoplastics for Compliant Mechanisms – Application and Material Phenomena, Advanced Engineering Materials 18(3) (2015) |
[2] |
SAXENA, A.: Synthesis of Compliant Mechanisms for Path Generation using Genetic Algorithm, Journal of Mechanical Design, 127 (2005), 745-752 |
[3] |
SHARMA, D.; DEB, K.; KISHORE, N.N.: Towards Generating Diverse Topologies of Path Tracing Compliant Mechanisms Using A Local Search Based Multi-Objective Genetic Algorithm Procedure, Proceedings of the World Congress on Computational Intelligence (WCCI-2008), (Hong Kong), Piscatway: IEEE Press . pp. 2004-2011 |
Kontakt
Institut für Leichtbau und Kunststofftechnik (ILK), Professur für Funktionsintegrativen Leichtbau, Fakultät Maschinenwesen der TU Dresden
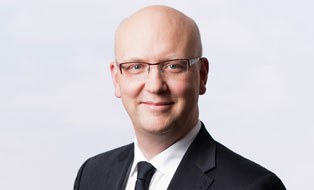
Professur für Funktionsintegrativen Leichtbau
NameProf. Dr.-Ing. Niels Modler
Eine verschlüsselte E-Mail über das SecureMail-Portal versenden (nur für TUD-externe Personen).
Institut für Leichtbau und Kunststofftechnik
Besucheradresse:
DÜR, Etage 0, Raum 69 Holbeinstr. 3
01307 Dresden
Deutschland