Promotionsprojekt 9: Mehrvariable robuste Regelung für räumliche Deformationen von I-FEV
Inhaltsverzeichnis
Motivation
Bei einer räumlichen Deformation gibt es Beeinflussungen zwischen physikalischen Eigenschaften in verschiedenen Deformationsrichtungen, die sich durch Mehrgrößenregler entkoppeln lassen. Die mechanischen Eigenschaften können sich richtungsabhängig ändern (z.B. Wirkungsrichtung einer Kraft unter einer Verdrehung) und damit ein stark nichtlineares Verhalten hinsichtlich des Verformungszustandes hervorrufen. Der Deformationszustand soll mit integrierter Sensorik detektiert werden und durch robuste, echtzeitfähige Regelalgorithmen gezielt und reproduzierbar einstellbar sein.
Stand der Forschung und eigene Vorarbeiten
In der Literatur existieren zahlreiche Beschreibungen zur eindimensionalen Lageregelung mit Aktoren auf Basis von Formgedächtnislegierungen [1]. In der 1. Kohorte wurden für die eindimensionale Deformation von Faser-Elastomer-Verbunden verschiedene Modelle auf Basis der theoretischen sowie der experimentellen Prozessanalyse entwickelt. Neben Modellen für das nominelle Verhalten entstanden bisher auch Modelle für Unbestimmtheiten, die sich aus Fertigungstoleranzen, sich ändernden Betriebsbedingungen (Zug, Druck, Temperatur) und Alterung ergeben. Auf Basis dieser Systembeschreibungen wurden robuste Regler entworfen und an verschiedenen Proben von Faser-Elastomer-Verbunden experimentell erprobt [2]. Der robuste Reglerentwurf erfolgt Offline, die zu implementierenden Regelalgorithmen sind echtzeitfähig [3]. Zusätzlicher Forschungsbedarf besteht hinsichtlich der Verallgemeinerung dieser Entwurfsmethoden für mehrdimensionale Lageregelungen.
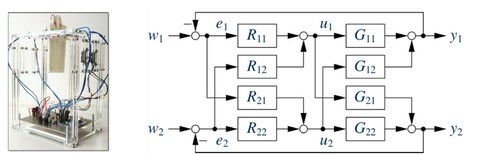
Versuchsstand (links), Strukturbild Mehrgrößenregelung (rechts)
Wissenschaftliche Fragestellung und Projektziele
Eine räumliche Deformation lässt sich durch mehrere, örtlich bzw. räumlich getrennte Stelleingriffe gezielt herbeiführen. Aus regelungstechnischer Sicht liegt damit ein Mehrgrößensystem vor, bei dem insbesondere auch Verkopplungen zwischen den verschiedenen Stellgrößen zu berücksichtigen sind. Eine Aufgabe des Mehrgrößenreglers ist dann auch die gezielte Entkopplung zwischen den Nebenregelstrecken [4]. Bei der Modellierung von Unbestimmheiten ergeben sich im Mehrgrößenfall auch deutlich mehr Freiheitsgrade. Für einen robusten Reglerentwurf sind daher geeignete und praktisch handhabbare Modellstrukturen für eine echtzeitfähige autarke Positionsregelung zu ermitteln. Bei der angestrebten großen und räumlichen Deformation treten auch aus geometrischer Sicht Nichtlinearitäten stärker in den Vordergrund. Hierzu sind neue Reglerstrukturen zu entwickeln und zu parametrieren. Hinsichtlich der Messwerterfassung soll der Fokus stärker auf in den Verbund integrierte Sensoren gelegt werden, so dass zusätzlich Filter und Schätzalgorithmen zu entwerfen und zu erproben sind.
Literatur
[1] | Ren, Z., Zarepoor, M., Huang, X., Sabelhaus, A. P., & Majidi, C. (2021). Shape Memory Alloy (SMA) Actuator With Embedded Liquid Metal Curvature Sensor for Closed-Loop Control. Frontiers in Robotics and AI, 8, 9. |
[2] | Keshtkar, N., & Röbenack, K. (2020). Unstructured uncertainty based modeling and robust stability analysis of textile-reinforced composites with embedded shape memory alloys. Algorithms, 13(1), 24. |
[3] | Zhou, K., & Doyle, J. C. (1998). Essentials of Robust Control. Upper Saddle River, NJ: Prentice Hall. |
[4] | Skogestad, S., & Postlethwaite, I. (2007). Multivariable feedback control: analysis and design. New York: Wiley. |
Kontakt
Institut für Regelungs- und Steuerungstheorie (RST), Fakultät Elektrotechnik und Informationstechnik der TU Dresden
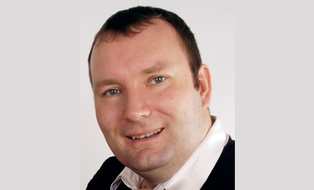
Professor
NameHerr Prof. Dr.-Ing. habil. Dipl.-Math. Klaus Röbenack
Institutsdirektor
Eine verschlüsselte E-Mail über das SecureMail-Portal versenden (nur für TUD-externe Personen).
Zertifikat der DFN-PKI für verschlüsselte E-Mails.
SHA1 Fingerprint: 5D:0B:FB:6F:92:2B:87:36:F5:F5:F0:48:64:77:66:8C:DB:58:56:7A
Institut für Regelungs- und Steuerungstheorie
Institut für Regelungs- und Steuerungstheorie
Besuchsadresse:
Institutsgebäude S7a, Raum 405 (Sekretariat 406) Georg-Schumann-Straße 7a
01187 Dresden