Subproject 10: Detection of microstructural damage in interactive fiber rubber composites by use of in situ imaging processes and development of criteria for damage prediction
Table of contents
Motivation
After the detection and analysis of global and local deformation, the definition of failure criteria as well as load limits for one-time and repeated mechanical loading, the focus has now shifted to investigating damage in active elements on the microstructural level. This requires the evaluation of interactions between initial material defects and load induced damage phenomena. Functional failure of I-FRC based on dielectric elastomer actuators is typically caused by electrical short-circuits occuring on electrodes. In order to reliably predict not only functional reliability, but also structural integrity of I-FRC, particularly in terms of 3D deformations with numerous cycles, potential crack formation in a fiber-reinforced elastomer matrix due to air inclusion and filler agglomeration must be taken into account. Hence, the reliable prediction of microstructural damage phenomena is key to ensuring long-term functional stability of I-FRC.
State of the art and preliminary research
Active I-FRC elements, particuluary dielectric elastomer actuators (DEA), have been the subject of intensive research in the field of electroactive polymers since the beginning of the 21st century [1–3]. Electrical breakdown is the most common reason for structural failure and has therefore been researched in detail [4–6]. The use of DE actuators for biomimetic applications is currently being researched in the applicant´s subproject [7, 8] where the damage behavior und material properties are investigated for a one-time deformation process. Within the 1st cohort, methods and processes for the 360° investigation of deformation behavior using digital image correlation and 12 cameras were established [9]. These methods enable the spatially resolved characterization of deformation behavior for complex I-FRC structural elements. However, a decisive factor for long-term DEA applications is the reliable prediction of process-structure property correlations as a result of repeated mechanical deformation - the present lack of knowledge on resulting relations suggests that there is a considerable need for research.
Scientific questions and project objectives
This subproject is aimed at subjecting the developed materials to repeated mechanical deformation in order to define the time and place of damage using, for example, multi-camera image correlation. Subsequent microstructural investigations using REM will then be employed to determine the type of damage and underlying mechanisms. Based on the data obtained, correlations between the type of loading and damage mechanism will be identified. In contrast to the work of the 1st cohort, upcoming analyses will include not only crack formation, but also crack growth within the elastomer matrix as well as in active elements. Therefore, it is essential to determine the speed of cracking for modified and basic materials by means of high-speed recordings. At the end of the 2nd cohort, comprehensive results regarding microstructural damage progress and underlying process-structure-correlations will be available.
References
[1] | O’Halloran A, O’Malley F, McHugh P. A review on dielectric elastomer actuators, technology, applications, and challenges. J. Appl. Phys. 2008; 104(7):71101. doi: 10.1063/1.2981642. |
[2] | Rudolph A, Ayers J, Davis JL. Neurotechnology for biomimetic robots. Cambridge, Mass: MIT Press; 2002. |
[3] | Bar-cohen Y. Electroactive polymers as artificial muscles - Reality and challenges. In: 19th AIAA Applied Aerodynamics Conference. Reston, Virigina: American Institute of Aeronautics and Astronautics; 06112001. S. 1 doi: 10.2514/6.2001-1492. |
[4] | Plante J-S, Dubowsky S. Large-scale failure modes of dielectric elastomer actuators. International Journal of Solids and Structures 2006; 43(25-26):7727–51. doi: 10.1016/j.ijsolstr.2006.03.026. |
[5] | Gatti D, Haus H, Matysek M, Frohnapfel B, Tropea C, Schlaak HF. The dielectric breakdown limit of silicone dielectric elastomer actuators. Appl. Phys. Lett. 2014; 104(5):52905. doi: 10.1063/1.4863816. |
[6] | Gisby TA, Xie SQ, Calius EP, Anderson IA. Leakage current as a predictor of failure in dielectric elastomer actuators. In: Electroactive Polymer Actuators and Devices (EAPAD) 2010: SPIE; 2010. S. 764213 (SPIE Proceedings). doi: 10.1117/12.847835. |
[7] |
Pfeil S, Katzer K, Kanan A, Mersch J, Zimmermann M, Kaliske M et al. A Biomimetic Fish Fin-Like Robot Based on Textile Reinforced Silicone. Micromachines (Basel) 2020; 11(3). doi: 10.3390/mi11030298. |
[8] | Pfeil S, Henke M, Katzer K, Zimmermann M, Gerlach G. A Worm-Like Biomimetic Crawling Robot Based on Cylindrical Dielectric Elastomer Actuators. Front Robot AI 2020; 7:9. doi: 10.3389/frobt.2020.00009. |
[9] | Katzer K. Digitale Bildkorrelation zur Validierung des Deformationsverhaltens von Interaktiven Faser-Elastomer-Verbunden. In: Werkstoffe und Bauteile auf dem Prüfstand: Prüftechnik - Kennwertermittlung - Schadensvermeidung; 2020 doi: 10.48447/WP-2020-031. |
Kontakt
Institute of Materials Science (IfWW), Chair of Materials Mechanics and Damage Analysis, Faculty of Mechanical Science and Engineering at TU Dresden
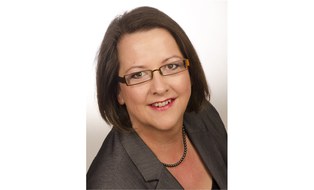
Ms Prof. Dr.-Ing. Martina Zimmermann
Inhaberin der Professur Werkstoffmechanik u. Schadensfallanalyse
Send encrypted email via the SecureMail portal (for TUD external users only).