Subproject 1: Development of innovative fibrous actuator and sensor mechanisms based on ionic electroactive polymers
Table of contents
Motivation
High-performance fibrous actuators are key to achieving 3D deformations in fiber composites by means of structually integrated mechanisms. These actuators can - just like natural musles - transform electrical energy into mechanical deformation, transmit high forces and provide large travel ranges. They offer particular advantages since actuators and sensors are based on almost identical mechanisms of action. Therefore, fibrous actuator structures can be employed as structurally compatible sensors for the in situ detection of strain, deformation and degradation.
State of the art and preliminary research
Planar actuators based on electroactive polymers (EAP) have been a prominent research topic [1, 2], particularly due to their high pitch dynamics (> 10 Hz) and the resulting spectrum of properties making them suitable for specific applications. Within the 1st cohort of the RTG 2430, fibrous EAP, specifically the subgroup of dielectric elastomer actuators (DEA), have been investigated in detail [3]. The focus was on their creation through spinning technology as well as the evaluation of the achieved actuator properties. The elastic and electrically conducting filaments that are required for actuators simultaneously offer the potential for use in sensor applications [4]. However, the usable actuator effect of DEA fiber configurations is currently limited. Therefore, the 2nd cohort will focus on researching fibrous actuator/sensor mechanisms based on ionic EAP, particularly by using intrinsically conducting polymers (CP), such as poly(3,4-ethylenedioxythiophene) (PEDOT) or polyaniline (PAni). They are, similar like the DEA investigated in the 1st cohort, able to achieve high transformation frequencies (in the range of 10 Hz), forces (> 1 N) and deformations (> 35 %), while simultaneously requiring a significantly lower activation voltage of approx. 10 V compared to DEA (> 5 kV) [5]. In contrast to DEA, they can expand or contract in a targeted manner according to specific potentials and even achieve bending movements in case of particular configurations; this represents an enormous advantage for the desired 3D deformations of the 2nd cohort. Fibrous CP actuators require an electrolyte for ion transport in addition to the actuator CP component, preferably in the form of a solid state electrolyte (e.g. based on polyethylene oxide). While the CP actuator itself serves as both strain and deformation sensor, an external sensor layer must be added in order to detect adjacent degradations, such as cracks. There is still a considerable demand for research regarding the design of the complete system, reproducible and functional technological processing and the systematic evaluation of the property spectrum.
Scientific questions and project objectives
The objective of SP 1 is to research and identify the properties of structurally integrated adjustable fibrous sensors and actuators based on innovative CP, thus establishing a solid knowledge base for customized ionic EAP. For the realization of complex fiber structures containing several components, interactions between chemical modifications of the polymeric base material (e.g. additives or fillers), the resulting interfaces and the structure-property relationships regarding different textile production processes, including solvent wet spinning, braiding and coating, must be systematically investigated. Moreover, the geometric, mechanical and electrical material properties of ionic EAP will be analyzed experimentally, based on which a material model will be derived establishing a foundation for SP 2 and SP 6.
References
[1] | Pfeil, S.; Henke, M.; Katzer, K.; Zimmermann, M.; Gerlach, G. A Worm-Like Biomimetic Crawling Robot Based on Cylindrical Dielectric Elastomer Actuators. Front. Robot. AI 2020, 7, 41101, doi:10.3389/frobt.2020.00009. |
[2] | Pfeil, S.; Katzer, K.; Kanan, A.; Mersch, J.; Zimmermann, M.; Kaliske, M.; Gerlach, G. A Biomimetic Fish Fin-Like Robot Based on Textile Reinforced Silicone. Micromachines (Basel) 2020, 11, doi:10.3390/mi11030298. |
[3] | Probst, H.; Lohse, F.; Cherif, C.; Kimura, M.; Katzer, K. Fiberbased Actuator Approaches for Smart Textile Structures. Tokyo (Japan), October 11, 2019. |
[4] | Probst, H.; Katzer, K.; Nocke, A.; Hickmann, R.; Zimmermann, M.; Cherif, C. Melt Spinning of Highly Stretchable, Electrically Conductive Filament Yarns. Polymers (Basel) 2021, 13, 590, doi:10.3390/polym13040590. |
[5] | Mirvakili, S.M.; Hunter, I.W. Artificial Muscles: Mechanisms, Applications, and Challenges. Adv. Mater. Weinheim. 2018, 30, doi:10.1002/adma.201704407. |
Contact
Institute of Textile Machinery and High Performance Material Technology (ITM), Faculty of Mechanical Engineering, TU Dresden
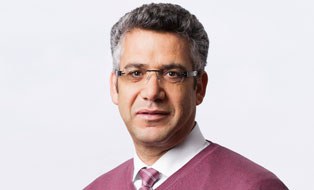
Mr Univ.-Prof. Dr.-Ing. habil. Dipl.-Wirt. Ing. Chokri Cherif
Head of the Institute and the Chair of Textile Technology
Send encrypted email via the SecureMail portal (for TUD external users only).