Subproject 8: Electro-mechanical modeling and metrological investigation of helical actuators with integrated sensor systems
Table of contents
Motivation
Interactive fiber rubber composites require actuators that offer significantly larger deformations and forces compared to the state of the art. Within the 1st cohort, the general potential of helical actuators as alternative approach for the integration of active fibers in elastomer composites was discussed. Initial experiments revealed that significantly increased deformations can be achieved. For this purpose, electroactive materials are of particular interest due to their quick response. The maximum force of a dielectric elastomer actuator could be further increased by means of materials that are stiffer than previously used elastomers. Moreover, in the case of helical actuators, properties such as maximum force and deformation can be specifically adjusted through the constructive parameters of the helical shape.
The relation between form and behavior is complex and highly dependent on the actuator concept and the manufacturing process. This subproject is aimed at (i) modeling the (thermo-)electro-mechanical behavior of helical actuators, (ii) deriving guidelines for optimal actuator design, (iii) finding options for the implementation of other material combinations and (iv) integrating sensors into actuators that enable the efficient monitoring of three-dimensional deformation behavior.
State of the art and preliminary research
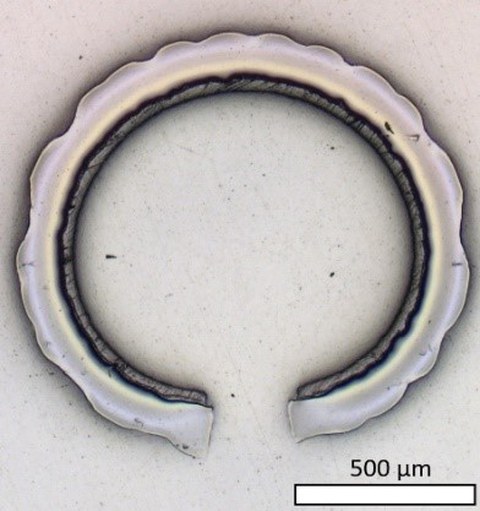
Helical dielectric actuator [1, 2]
As a result of preliminary research [1, 2], a demonstrator for a helical dielectric actuator (see Fig.) was manufactured, thus proving that the deformation potential of an actuator can be increased by at least one order of magnitude when a helical shape is implemented. Additionally, it was demonstrated that the actuator can simultaneously serve as strain sensor. It was also revealed that the electrical resistance is highly dependent on the strain applied. In addition to electroactive polymer actuators, thermoactive polymer actuators made of highly twisted monofilaments were also produced. A combination of electro- and thermoactive components would offer additional freedom for the realization of 3D motion.
Scientific questions and project objectives
To investigate the behavior of electro- (and thermo-)active helical actuators (SP1 and SP2), electro-thermo-mechanical network models for the calculation of force and deviation based on material and geometrical parameters must be developed. Corresponding demonstrators must be validated experimentally and compared to the models. Furthermore, it will be investigated where and how sensor structures can be integrated to ensure the precise monitoring of deformation and potential damage due to excessive strain. Other objectives include the development of innovative bisensitive actuator structures that are electroactive as well as thermoactive.
References
[1] | J. Mersch, M. Koenigsdorff, A. Nocke, C. Cherif, G. Gerlach: High-speed, helical and self-coiled dielectric polymer actuator. Actuators 10 (2021), 15 (10 pages). |
[2] | J. Mersch, M. Koenigsdorff, A. Nocke, C. Cherif, G. Gerlach: Manufacturing of a helical, self-coiling delectric polymer actuator. Proceedings 64 (2020), 38 (7 pages). |
Contact
Institute of Solid State Electronics (IFE), Faculty of Electro and Computer Engineering at TU Dresden
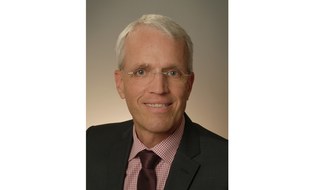
Mr Prof. Dr.-Ing. habil. Gerald Gerlach
Institutsdirektor
Send encrypted email via the SecureMail portal (for TUD external users only).
Visiting address:
Günther-Landgraf-Bau 7-E01b Mommsenstraße 15
01069 Dresdem
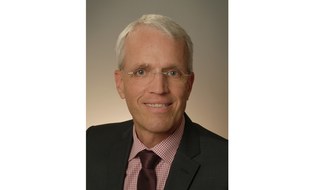
Mr Prof. Dr.-Ing. habil. Gerald Gerlach
Institutsdirektor
Send encrypted email via the SecureMail portal (for TUD external users only).
Visiting address:
Günther-Landgraf-Bau 7-E01b Mommsenstraße 15
01069 Dresdem