AI-supported acoustic emission monitoring for automatic damage detection in supporting structures of wind turbines
Table of contents
Project data
Titel | Title KI-unterstütztes Schallemissionsmonitoring zur automatischen Schadenserkennung in Tragstrukturen von Windenergieanlagen | AI-supported acoustic emission monitoring for automatic damage detection in supporting structures of wind turbines Projektnummer | Project number 0524 Förderer | Funding Bundesministerium für Wirtschaft und Energie (BMWi) / KISWind Zeitraum | Period 01.07.2020 – 30.06.2023 Leiter | Project Manager Prof. Dr.-Ing. Steffen Marx Bearbeiter | Contributors Dipl.-Ing. Ronghua Xu Projektpartner | Project Partner Leibniz Universität Hannover; Max Bögl Wind AG; MKP GmbH; TÜV Süd Industrie Service GmbH |
Short description
The overall objective of the research project is the development of methods for efficient and automated continuous monitoring of the support structure of wind turbines for the detection of damage events and anomalies using acoustic emission analysis and innovative evaluation methods from the field of artificial intelligence (AI).
Report in the annual report 2020
AUTOMATIC STRUCTURAL HEALTH MONITORING SYSTEM OF WIND TURBINES
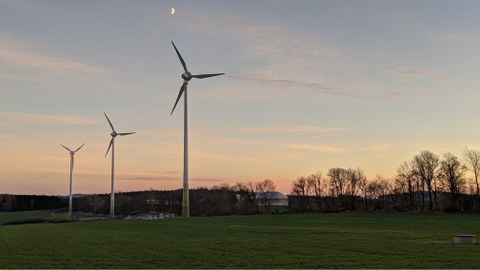
Wind turbines in the easter ore mountain range
In 2018, the Federal Ministry for Economic Affairs and Energy (BMWi) demanded in the sixth monitoring report of the energy transition that by 2050 at least 80% of greenhouse gas emissions should be reduced and at the same time a share of 60% of renewable energies in the gross final consumption of energy should be achieved compared to 1990. With around 16% participation in total energy generation in Germany, wind energy is one of the focal points of the energy transition. To be able to meet the goal, on the one hand, the performance of the wind turbines must be increased and, on the other hand, their construction and maintenance costs must be reduced. For lower maintenance costs, damage to components must be detected on time before they cause a critical failure and require costly repairs. The basis for this type of maintenance is data that contain information about changes in condition and damage.
For the wind turbines in operation, most of the data is obtained using conventional measurement methods, e.g. strain gauges or acceleration sensors. With this method, however, it is assumed that sufficiently large damage causes global structural deformation in the structure or in components, which can be recorded by the above-mentioned
measurement technology. Small damage that has occurred cannot be identified and localized in time with this method.
In this project, acoustic emission measurements are used to generate data that enables the damage events to be detected directly. A large number of large-scale experiments are planned in the Otto Mohr laboratory of the TU Dresden in which the generated wire break signals of tendons are recorded by acoustic emission sensors. Various influencing parameters are investigated during the tests, such as different sensor arrangements,
distances between breakpoints and sensors. The determined data is processed with the help of the new evaluation methods from the field of artificial intelligence (AI). Based on the findings, a concept for an effective structural health monitoring system (SHM system) for wind turbines should be developed, which can provide information about the condition of the load-bearing structures.