Subproject 2: Simulation-based development of textile reinforcement structures for adaptive rubber composites with multi-sectional solid state joints
Table of contents
Motivation
To create fiber-reinforced composite structures that are capable of multi-joint and spatial motions, solid state joints must be arranged in a sequential manner, including various degrees of freedom and preshaped geometries that can adopt bistable states, while simultaneously offering complex mechanisms of action, for example in the form of bending-torsion switching elements. Integral textile-technological manufacturing technologies are used to ensure the proper positioning of reinforcement fibers and actuators according to specific requirements as well as the integration of conductor tracks and the contacting of actuators. In this context, the modeling process based on the finite element method is of particular importance since it provides information on the appropriate arrangement of functional components, thus ensuring the desired mechanisms of action. Hence, a meso scale modeling approach is required that unites both the actuator as well as the textile reinforcement structure and that can represent three-dimensional mechanisms.
State of the art and preliminary research
Soft elastomer matrices with structurally integrated actuators allow for large reversible deformations without the need for additional external drives [1 – 5]. Hence, extensive research efforts of the 1st cohort were directed to fiber-reinforced elastomer composites containing an elastomer matrix with glass fiber reinforcement and integrated actuators that are suitable for textile processing and made of a nickel-titanium shape memory alloy (SMA). Based on the material data of individual components determined by thermomechanical characterization, meso scale simulation models for two-dimensional reinforcement structures [6] were generated that provide specific predictions for the motion behavior at the structural level based on parameter studies. As a result, these models enabled the structural design of specific motion tasks, see image. This established the foundation based on which the step-by-step manufacturing of actively deformable samples was realized using multi-layer knitting technology and infiltration processes. These samples were then analyzed in terms of their deformation behavior by the defined activation of integrated actuators and subsequently used for the validation of simulation models. However, there is a considerable need for research regarding the design and development of textile actuator structures for spatially evolving and gradual motions.
Scientific questions and project objectives
The objective of SP 2 as part of the 2nd cohort will be the investigation of adaptive elastomer composites with functionally adaptable, textile-based actuators to determine their suitability for three-dimensional mechanisms, including bending-torsion coupling (2 degrees of freedom within one joint), the realization of multi-joint structures (at least 3 sequentially arranged joints in one structure) and the use of bistable states for fast switching operations (> 10 Hz). Moreover, SP 2 will be aimed at the integration of conducting tracks and the contacting of textile actuators. Based on the modeling of individual components, a robust meso scale modeling approach will be developed and validated that will enable the representation of complex mechanisms and 3D deformation patterns, especially when using alternative actuator materials besides SMA, such as the electroactive polymers (EAP) employed in SP 1.
References
[1] | Kazemi Lari, M. A.; Dostine, A. D.; Zhang, J.; Wineman, A. S.; Shaw, J. A.: Robotic jellyfish actuated with a shape memory alloy spring. (2019), S. 2 f. |
[2] | Wang, W.; Rodrigue, H.; Ahn, S.-H.: Deployable Soft Composite Structures. Scientific reports 6(2016), p. 20869 |
[3] | Huang, X.; Kumar, K.; Jawed, M. K.; Mohammadi Nasab, A.; Ye, Z.; Shan, W.; Majidi, C.: Highly Dynamic Shape Memory Alloy Actuator for Fast Moving Soft Robots. Adv. Mater. Technol. 4(2019)4, S. 1800540 f. |
[4] | Kim, H.-I.; Han, M.-W.; Song, S.-H.; Ahn, S.-H.: Soft morphing hand driven by SMA tendon wire. Composites Part B: Engineering 105(2016), S. 138-148 |
[5] |
Lee, J.-H.; Chung, Y. S.; Rodrigue, H.: Long Shape Memory Alloy Tendon-based Soft Robotic Actuators and Implementation as a Soft Gripper. Scientific reports 9(2019)1, p. 11251 |
[6] | Felix Lohse; Henriette Probst; Moniruddoza Ashir; Chokri Cherif; Rico Hickmann: Modeling of adaptive systems for interactive Fiber Rubber Composites. AUTEX 19th World Textile Conference 2019, |
Contact
Institute of Textile Machinery and High Performance Material Technology (ITM), Faculty of Mechanical Engineering, TU Dresden
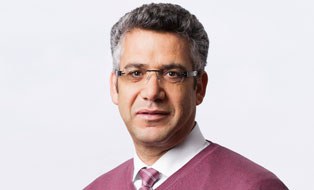
Mr Univ.-Prof. Dr.-Ing. habil. Dipl.-Wirt. Ing. Chokri Cherif
Head of the Institute and the Chair of Textile Technology
Send encrypted email via the SecureMail portal (for TUD external users only).