Fuzzy-stochastic methods for polymorphic uncertainty in lightweight structures
A continuation of the topic is currently taking place in the second project phase.
The overall goal of this proposal is the consideration of polymorphic uncertainty for modeling of lightweight structures. As a prototype material we consider a unidirectional fiber-reinforced composite, where uncertainty in the data may be caused e.g. by heterogeneity of the material, incomplete or imprecise experimental data, irregularities in fabrication, changing boundary conditions etc. For this reason, different kinds of uncertainties need different characterization techniques, such as fuzzy, stochastic and/or fuzzy-stochastic. The related transversely isotropic behaviour is investigated with a single-scale and a two-scale approach. In particular, the following objectives are investigated:
-
Experimental characterisation is performed for the unidirectional fiber-reinforced composite. In particular we are interested in the mechanical behaviour of, firstly, the (anisotropic) composite, and secondly, the individual (isotropic) constituents of the composite, that is fiber and matrix. Additionally, the volume fractions of both constituents are determined.
-
Single- and two-scale modeling: The transversely isotropic behaviour is investigated with a single-scale and a two-scale approach. For the first model, the material parameters regarding anisotropy are identified from the experiments. For the latter analytical (Mori-Tanaka and Eshelby) and numerical (finite element method) schemes are used, in order to identify effective properties regarding the heterogeneous material structure for FRCs.
-
Stochastic finite element formulation: Based on the experiments and in combination with the generation of artificial data the probability distribution of (effective) material parameters for the single- and respectively the two-scale model will be determined. Formulating the material parameters as stochastic variables enables the formulation of stochastic finite element method (SFEM). In this context the stochastic variables are described by the Polynomial Chaos Expansion (PCE).
-
Fuzzy stochastic finite element: The polymorphic uncertainty is taken into account with the fuzzy stochastic finite element method (FSFEM), which is a combination of the fuzzy finite element method (FFEM) and the stochastic finite element method (SFEM). To this end, the PC coefficients are described as fuzzy variables. Therefore, it is important to understand the dependencies respectively the interactions of the fuzzy stochastic variables.
-
Evaluation: Finally, both approaches, the single-scale and two-scale model, are compared with respect to e.g. uncertainty of the system response, sensitivity of material parameters, geometrical parameters etc. Using this knowledge an improved material design becomes possible.
Summary of the Results
In the course of the first funding period, a basic framework was created to take polymorphic uncertainties into account in the modeling of lightweight structures. In particular, fiber-reinforced plastics (FRP) were investigated in which uncertainties occurs e.g. due to the heterogeneity of the material, incomplete experimental data, irregularities in production, changing boundary conditions, etc. In order to describe structures with polymorphic uncertainties, the fuzzy FEM (FFEM) and the stochastic FEM (SFEM) were combined to form the fuzzy stochastic FEM (FSFEM).
A transversely isotropic material was investigated as a prototype, using one-scale and two-scale models. The material behavior was first reproduced using a linear elastic transversely isotropic material model and the associated five independent material parameters, which corresponds to a one-scale model. Experimental investigations were carried out on the composite to determine all five required material parameters. This includes tensile and shear tests on FRP with different fiber orientations.
For the two-scale model, analytical (Mori-Tanaka and Eshelby) and numerical (finite element) homogenization methods were used to calculate effective quantities to take into account the heterogeneous structure of the FRCs. As a basis for the homogenization, the individual components of the composite, i.e. the fiber and the surrounding matrix, are considered separately. In the first approach, both components were modeled in a linear, elastic, isotropic manner. In this context, the required parameters of the individual components, i.e. carbon fibers and epoxy resin, could be identified with the help of tensile tests. In order to be able to determine the fiber volume fraction of the fibers in the composite, additional investigations, such as the ashing of the matrix in the composite, were carried out.
Since the FSFEM were characterized by fuzzy uncertainties, which is based on fuzzy random variables and / or fuzzy random fields, the polynomial chaos expansion (PCE) was used. The PCE was modified in such a way that the classically deterministic PC coefficients can also be used in the modeling as fuzzy PC coefficients. With this, different types of uncertainties as well as polymorphic uncertainties of the (effective) material parameters can be described in the one-scale and in the two-scale model. In addition to the uncertain material parameters, the FEM discretization has been adapted so that it is also possible to take into account fuzzy geometric variables, such as the fiber diameter in the numerical homogenization.
In order to show the versatility of the methods used, different uncertainty models were assigned to different variables and compared with one another. In addition, the one-scale model was compared with the different methods of the two-scale model and evaluated. Analytical (Mori-Tanaka and Eshelby) methods could not carry out sufficiently accurate homogenizations, especially with the higher fiber volume proportions. The numerical methods with a fine grid should therefore always be examined as a reference model.
Essential project findings
- Experimental characterisation for unidirectional FRP
- Single- and two-scale modeling of unidirectional FRP
- Stochastic finite element formulation
- Fuzzy-stochastic finite element formulation
- Analytical and numertical fuzzy-stochastic homogenazation methods
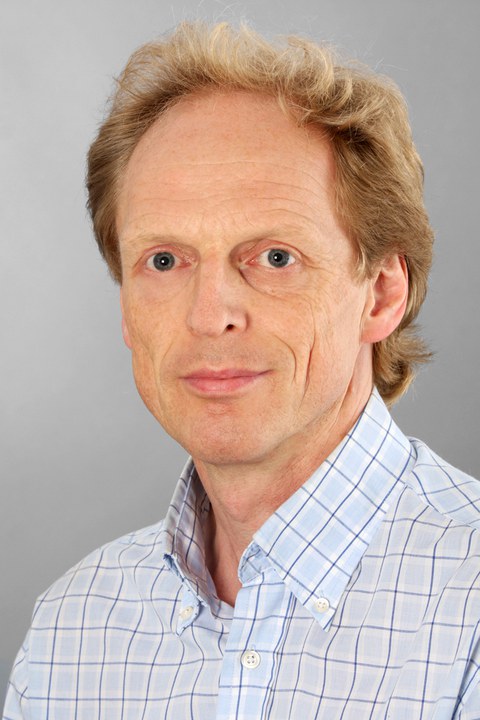
Prof. Mahnken
Prof. Dr.-Ing. Rolf Mahnken
Universität Paderborn
Fakultät für Maschinenbau
Lehrstuhl für Technische Mechanik
-
Mäck, M.; Caylak, I.; Edler, P.; Freitag, S. Hanss, M.; Mahnken, R.; Meschke, G.; Penner, E.: Optimization with constraints considering polymorphic uncertainties. Surveys for Applied Mathematics and Mechanics (GAMM-Mitteilungen), 2019, Link
-
E. Penner, I. Caylak, A. Dridger, and R. Mahnken. “A polynomial chaos expanded hybrid fuzzy-stochastic model for transversely fiber reinforced plastics”. Mathematics and Mechanics of Complex Systems 7.2 (2019), pp. 99-129.
-
R. Mahnken. “A variational formulation for fuzzy analysis in continuum mechanics”. Mathematics and Mechanics of Complex Systems 5.3 (2017), pp. 261–298.
-
A. Dridger, I. Caylak, R. Mahnken, and E. Penner. “A possibilistic finite element method for sparse data”. Safety and Reliability 38.1-2 (2019), pp. 58-82.
-
I. Caylak, E. Penner, A. Dridger, and R. Mahnken. “Stochastic hyperelastic modeling considering dependency of material parameters”. Computational Mechanics 62.6 (2018), pp. 1–13.