A stochastic approach to damage evolution in die-cast zinc alloys
A continuation of the topic is currently taking place in the second project phase.
ZAMAC (Zinc, Aluminum, Magnesium and Copper) alloys are frequently used in the common industrial branches like automotive, electronics, cabinetry and beyond. A common manufacturing process for ZAMAC is die-casting, which is characterized by forcing the molten alloy under high pressure into a mold cavity. The Siegenia-Aubi KG., a long time partner of our Solid Mechanics Chair, offers a wide range of components from hardware for windows and French windows to building technology for automation and intruder protection, many of them made out of ZAMAC.
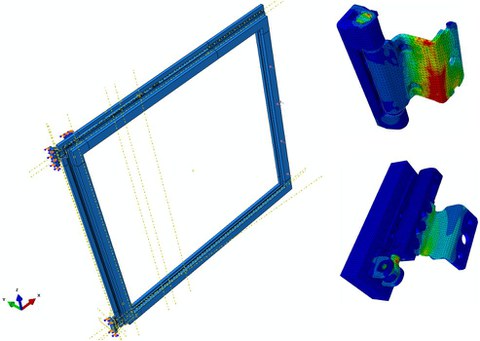
Typical ZAMAC components: CAE model of a window frame and finite element analysis of the stress distribution in the upper scissor bearing and the corner bearing at slamming, cf. [1]
Therefore, the material’s properties are of great interest.
From experience three phenomena are known in die-cast ZAMAC which result in a decay of its high strength and reliability:
-
reduction of strength in the course of time
-
creep deformation
-
dimensional change up to 1% as result of aging
All three phenomena are thermal activated processes and strongly depend on the operating temperature. From the industrial point of view such volume changes can be marginalized by tempering and thus we will not further consider it here.
Also, we do not plan to explicitly study creep deformation. Under isothermal conditions creep is a long term process of plastic deformation which has its origin in morphological changes,but is usually described phenomenologically. Here we will instead focus on aging in the sense of a decay of mechanical strength.
In total there is a good understanding of ideal ZAMAC from the material science point of view. Data on Zn-Al mixtures are available in chemical databases and using the CALPHAD method the Helmholtz free-energy of the alloy can be established. Limited knowledge, however, is available about the interaction of micromorphological evolution and the material’s structural behavior, in particular, regarding the decay of stiffness and the observed wide span of life expectation. Also, there are no reliable thermo-mechanical models which may be implemented in finite element programs in order to provide a predictive simulation tool. Such tools, however, are strongly needed by industry to determine the limit loads of their components. Despite of the widespread usage there are only few reliable data available regarding the long term behavior of ZAMAC casted components. It is known, that aging of the alloy starts already at room temperature and at loads exceeding 50 MPa. The very high mechanical properties diminish within one year - the more the higher the operating temperature is.
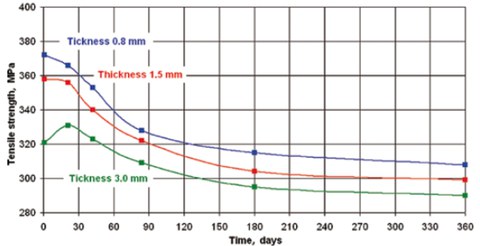
Decrease of tensile strength for Z410 during aging at room temperature as a function of time and wall thickness, from [2]
This motivates us to study the loss of mechanical strength in ZAMAC as a result of thermal aging and mechanical loading. To achieve this ambitious goal we will develop and employ an extended phase-field approach.
The overall goal of the research project is to predict the influence of thermal and mechanical loading on the aging of a typical industrial material stochastically within the following subgoals
-
develop a phase-field approach for void nucleation and growth under a simple deterministic driving force + an operator-scaling random field to model fluctuations from the ideal state
-
numerical implementation of a Markov chain for probabilistic modeling of void growth
-
formulate a phase-field model of ZAMAC
-
combine the models
-
perform extensive numerical studies in order to deduce and validate the resulting void distribution
-
use these results to derive first conclusions about the resulting mechanical properties of a ZAMAC casted component
Image sources:
[1] T. Dally and Weinberg. K. FEM-Simulation der Laibungsprüfung für Beschläge von Fensterflügeln. Abschlussbericht zum Projekt (unveröffentlicht), Siegenia Aubi KG, 2015
[2] L. H. Kallien and W. Leis. Ageing of zink alloys. International Foundry Research, 64(2): 23–27, 2011
Summary of the Results
A Markov chain model model to damage evolution was proposed. The Markov chain model describes the evolution of a characteristic size of the voids, e.g. a micro-crack length, a spall plane or a pore volume. The idea of the Markov chain model is now to describe the transition of the defect distribution from a time t to the next time t + dt, i.e. to the next loading cycle, by means of a certain probability. Then, the Markov chain is applied to the initial distribution as long as some damage parameter is below a critical value Dt ≤ Dcrit. The results of our Markov chain simulation were in reasonable agreement with respect to the mean of the hinges’ lifetime. Further emphasis has to be put on the improvement of the transition probabilities p whose modeling should be physically motivated. With the help of the Siegenia Aubi KG we investigated typical ZAMAK components before and after fracture. In doing so, however, we found no evidence of void growth. Therefore we had to discard our plans of modeling the microstructural evolution of the alloy as a consequence of mechanical loading.
We then investigated a novel concept to model uncertainties, the data-driven FEA directly exploits the raw data of the experimental investigations in the finite element simulations. In general, the data-driven method is more intuitive than the modeling with a stochastic process in a stochastic FEA. Apart from that, the data-driven method yields only one result per data set because it is not a stochastic approximation. The stochastic FEA approach is easy to implement in an available finite element software once the stochastic process is set. However, the computations of the underlying stochastic partial differential equations are costly; particularly simple Monte Carlo sampling requires extensive computational power for complex applications. With the goal to model the large variations of ZAMAK’s strength and resistance we compared in our work the two finite element approaches regarding their ability to work with uncertain material data.
Essential project findings
- a Markov chain model for the change of the pore distribution was established
- in experiments the distribution at the beginning and at the end of the lifetime of window hinges could be determined
- the determination of the transition probabilities proved to be difficult
- in the further course, the focus was on data-driven simulations
- data-driven simulations can be used to implement uncertainties without a model
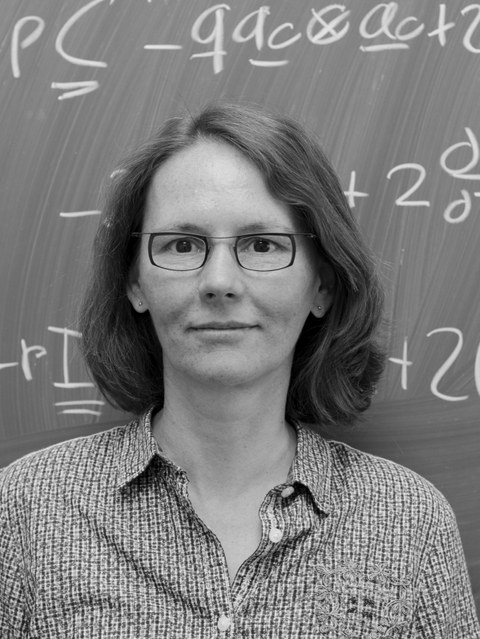
Prof. Weinberg
Prof. Dr.-Ing. Kerstin Weinberg
Universität Siegen
Fakultät IV
Department Maschinenbau
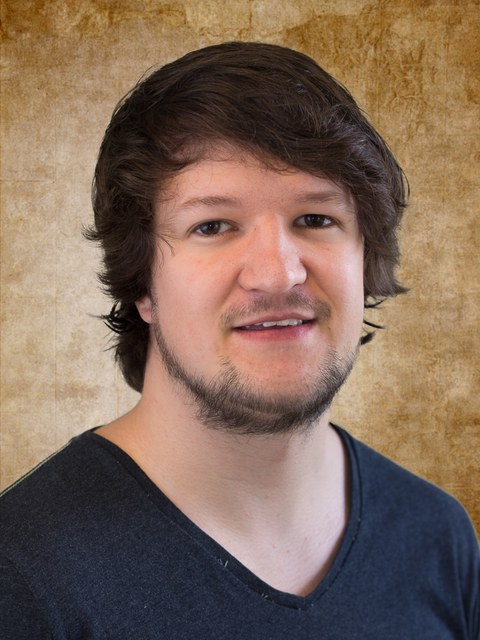
Hr. Korzeniowski
Tim Fabian Korzeniowski, M.Sc-Math.
Universität Siegen
Fakultät IV
Department Maschinenbau
- Korzeniowski, T. F.; Weinberg, K.; Drieschner, M.; Matthies, Hermann G.; Rosic, B.; Hoang, Truong V.; Srisupattarawanit T.; Brumme, S.; Müller, M.; Ostermeyer Georg P.; Henning, C; Ricken, T.:
Analysis of polymorphic data uncertainties in engineering applications,
(GAMM - Mitteilungen) 42.2, Wien 2019, Link - Korzeniowski, T. F.; Reppel, T.; Weinberg, K.:
A juxtaposition of data driven and stochastic finite element analyses for problems with noisy material data, Proceedings Applied Mathematics and Mechanics
(PAMM) 19.1, Link - Reppel, T.; Korzeniowski, T. F.; Weinberg, K.:
Effect of uncertain parameters on the deflection of beams, Proceedings Applied Mathematics and Mechanics (PAMM) 19.1, Link - Korzeniowski, T. F.; Weinberg, K.:
A comparison of stochastic and data-driven FEM approaches to problems with insufficient material data, Computer Methods in Applied Mechanics and Engineering 350 (2019) pp 554 - 570 - Korzeniowski, T. F.; Weinberg, K.:
Data-driven approch to elastic problems, Proceedings Applied Mathematics and Mechanics (PAMM) 18.1, Link - Korzeniowski, T. F.; Weinberg, K.; Markov, A.:
Chain Approach to Damage Evolution in Die-Cast ZAMAK. (2018). DOI: 10.24352/UB.OVGU-2018-025